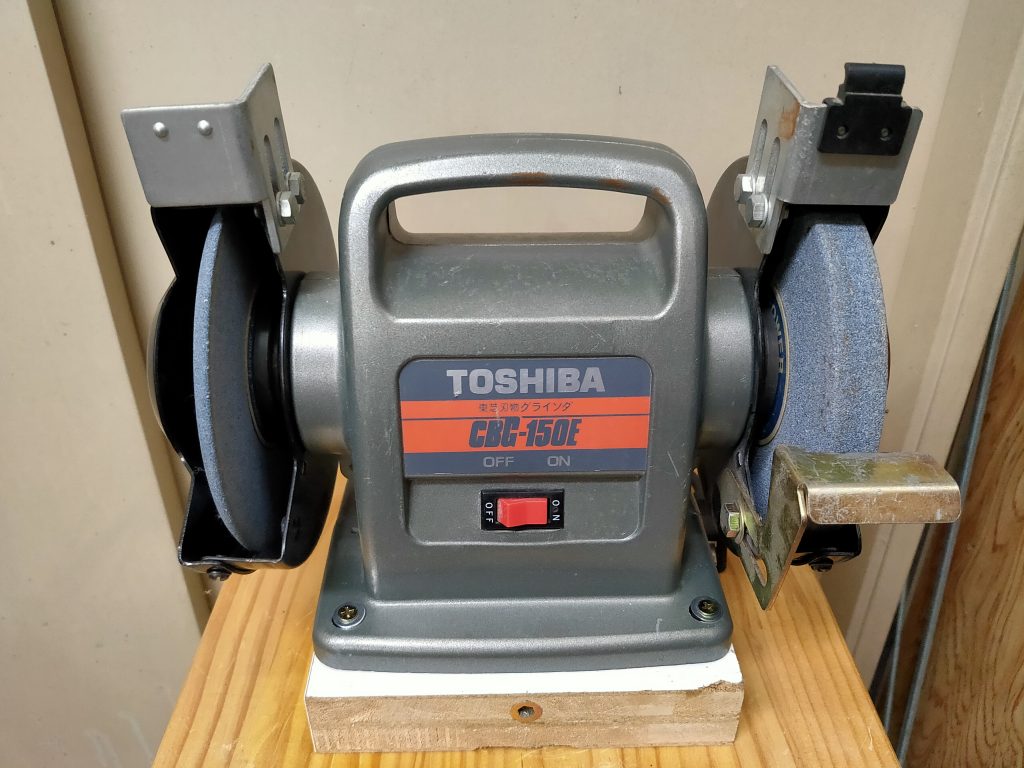
今回、ディスクサンダーを自作します。木工作業をしていると、ヤスリ掛けすることがよくあります。また、角を丸めたり面取りしたり、鋸で切ったときの木口を鉋掛けやヤスリ掛けをします。そういったときにディスクサンダーがあると、手軽に素早くきれいに加工することができ、欲しいなあと常々、思っていました。
そこで、工房にあるグラインダーを使って、ディスクサンダーを自作しようと思い立ちました。両頭グラインダーの片側をディスクサンダーにすると便利だと思いました。
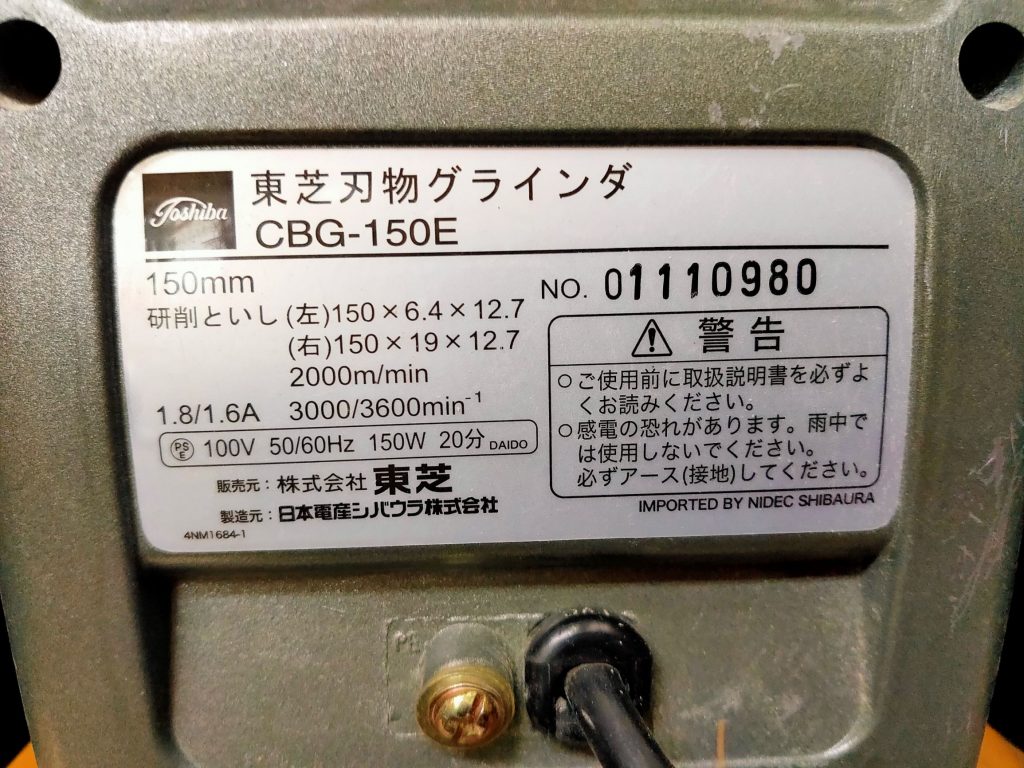
グラインダーの諸元を見ると、定格出力150W、60Hz地域なので定格回転速度3600r/minの単相モーターです。
ちょっと電気工事士の勉強。電源の周波数(f Hz)とモーターの同期回転速度(Ns r/min)の関係は、以下です。
同期回転速度 Ns = 120 × f / P
P:固定子の局数(極)
そうすると、このグラインダーの極数は、以下となります。
P = 120 × f / Ns = 120 × 60 / 3600 = 2 極
極数は、2,4,6と偶数となります。4極モーターの場合、回転速度は1800rpm(60Hz時)になり、6極だと1200rpm(60Hz)になります。この時トルクは、極数が多くなるほど、大きくなります。
この極数2のグラインダーでは、負荷がかかって回転速度が落ちるとトルクが小さくなり、そのまま負荷をかけ続けると止まってしまうので、負荷の大きい作業には使えません。止まったままにしていると電気エネルギーが熱に代わりモーターが焼けてしまいます。
電動工具を自作する場合は、モーターの選定が大事です。
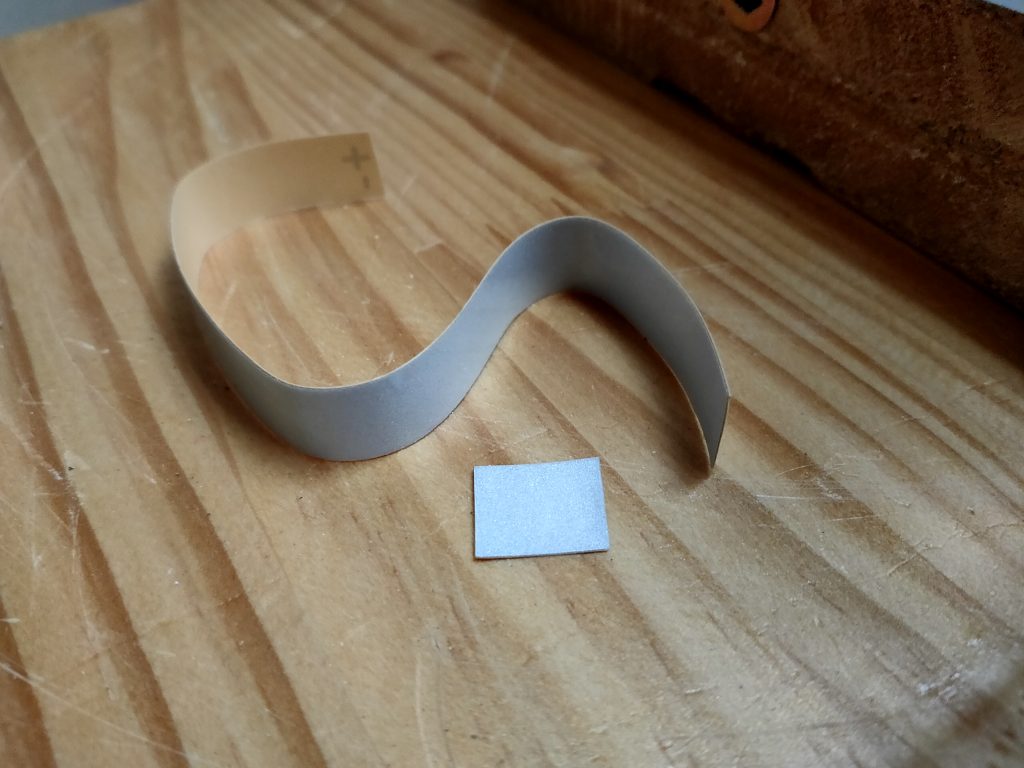
グラインダーの回転数を計測してみたいと思います。準備として、グラインダー回転面に写真の反射板シールを貼ります。
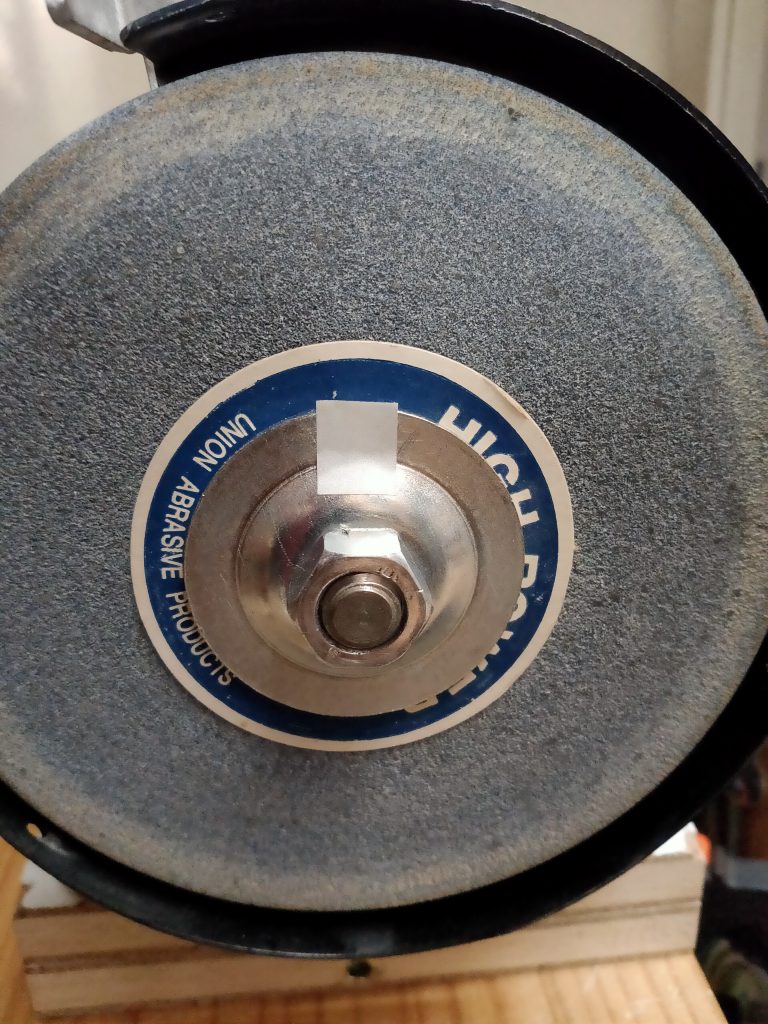
グラインダーの回転部に反射版シールを貼り付けました。この反射板にレーザー光を当てて回転数を計測します。
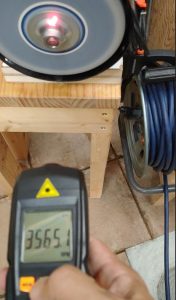
回転計でグラインダーの回転を計測しているところです。赤色レーザー光が照射されているのがわかりますが、目を傷めてしまうためレーザー光を見てはいけません。
回転計を手で持っているため、測定値は結構変化してしまいます。
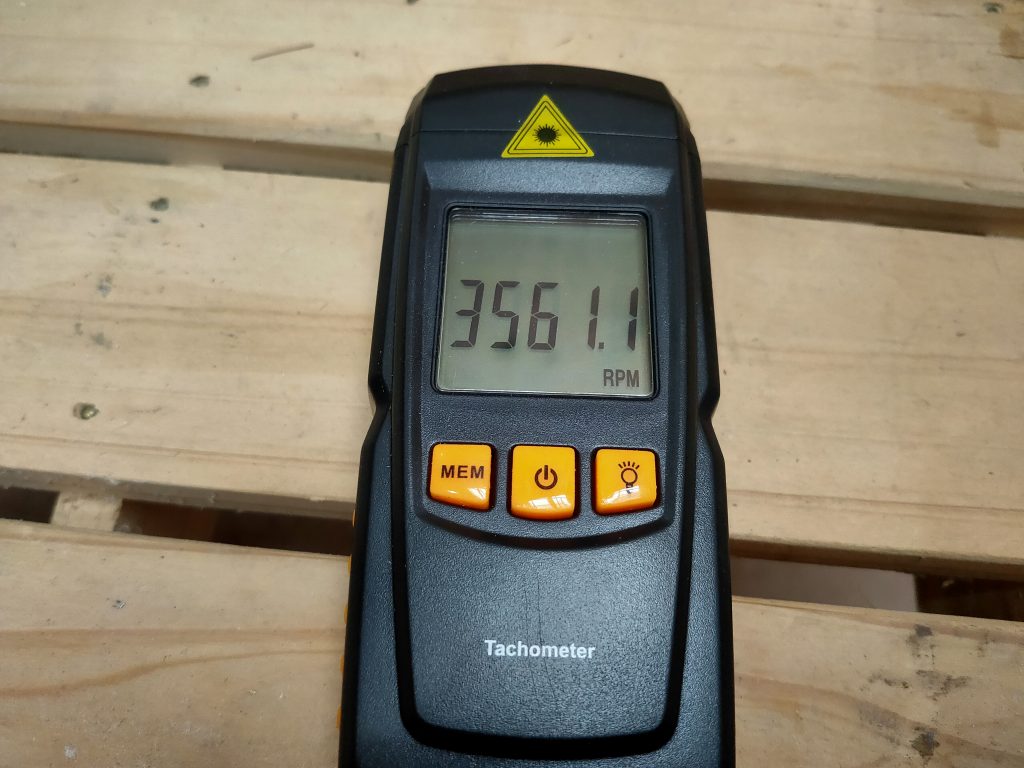
回転計(タコメーター)の中央黄色のスイッチを長押しすると、前方から赤色レーザー光を照射し、その反射光の間隔時間から回転数を割り出して表示します。
計測結果では、3561rpmで諸元の3600rpmに近い数値となっています。この差は「すべり」と言われるものです。「すべり」とは、誘導モーターにおいて、磁界の回転に対して、実際に回転子が回転するときの速度のズレのことを指し、百分率で表します。実際には回転計の測定誤差も含まれていると思います。
また、ちょっと勉強。ここで誤差がないとみなした場合のすべりを求めたいと思います。
すべり = (定格回転数 – 実回転数)/ 定格回転数
= (3600 – 3561) / 3600 × 100
≒ 1.08%
Webで調べたところ、三相モーターの場合、すべりは2~3%で小型単相モーターでは、これより大きいとのこと。そうすると、回転計のレーザーの当て方による誤差や回転計そのものの誤差を含めて、3%程度の誤差があるかもしれません。
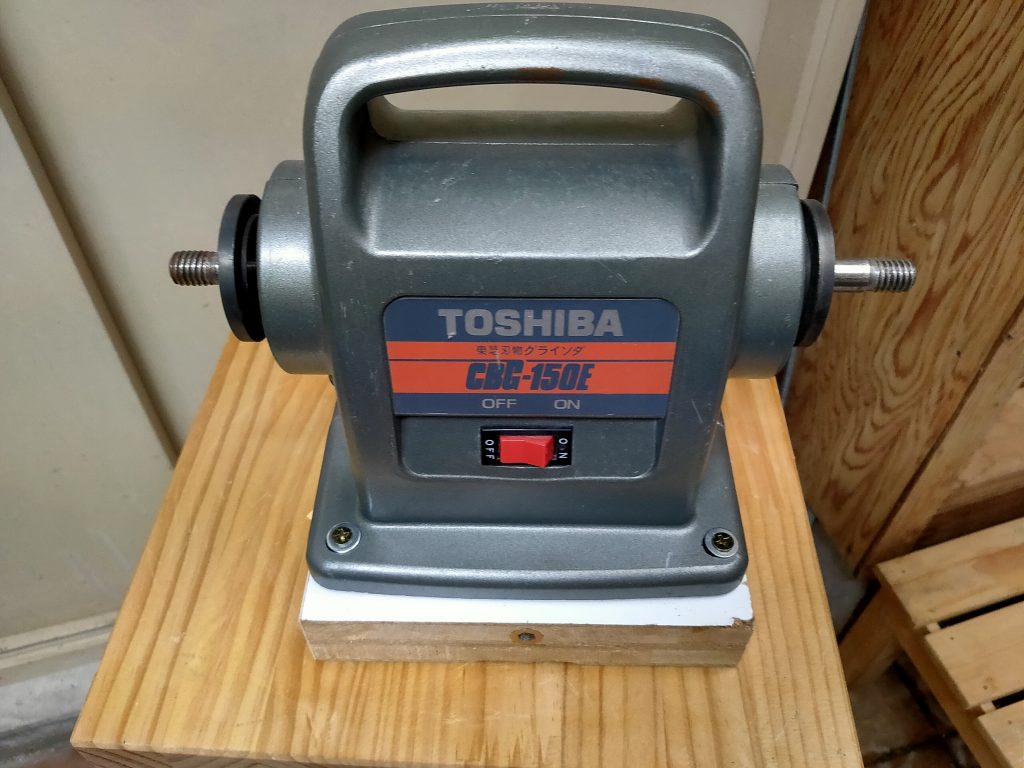
早速、ディスクサンダーの製作に取り掛かります。まずは、グラインダーの砥石と砥石カバーを取り外します。砥石は、回転時に緩まないように逆ネジで固定されているので、緩める向きを間違えないようにします。
写真は取り外した状態です。よく見ると、左右の軸の長さが異なります。2種類の厚みの異なる砥石を付けられるようにしてあります。どちらの軸にディスクサンダーを取り付けるかで設計寸法が変わります。今回は、左側の軸の短い方に取り付けることにしました。
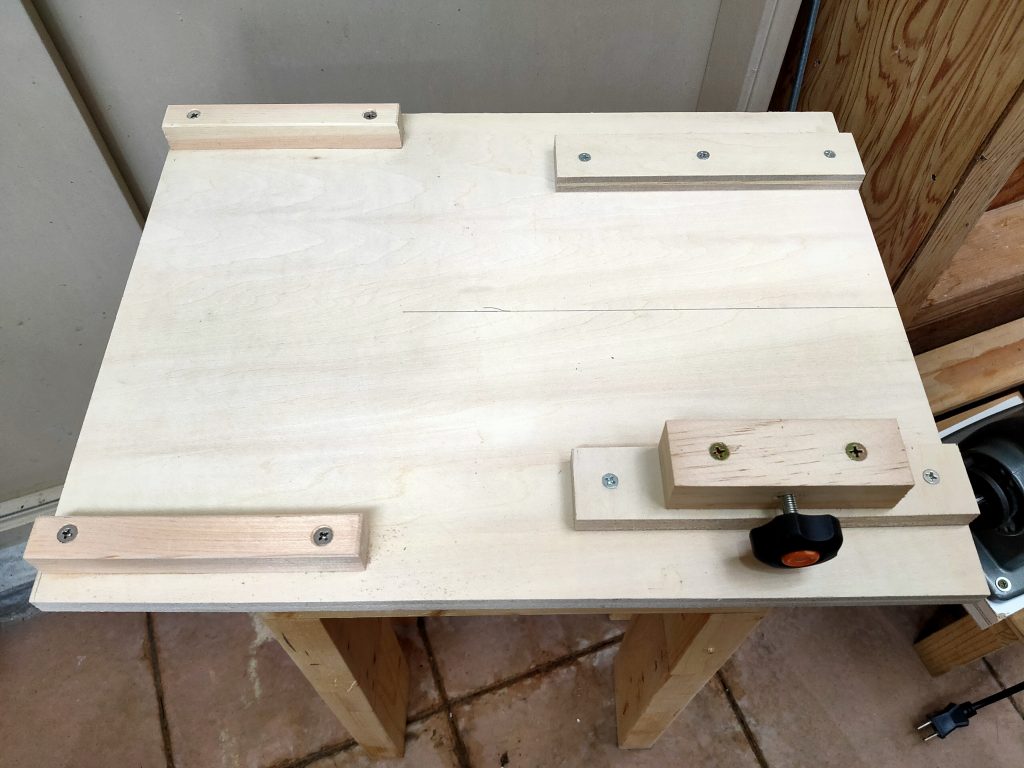
次に土台の部分を製作しました。グラインダー本体は写真右側に固定します。がっちり固定ではなく、保守のことも考えて取り外せるようにボルトで固定します。右下の取っ手を回して固定、取り外しできるようにしました。
前の写真のグラインダー本体の下部に板を取り付けています。その板の中央に鬼目ナットを埋め込んでいます。そのナットと土台のボルトで固定します。
なお、土台の寸法を設計するには、下述の内容を確認の上、寸法を決める必要があります。
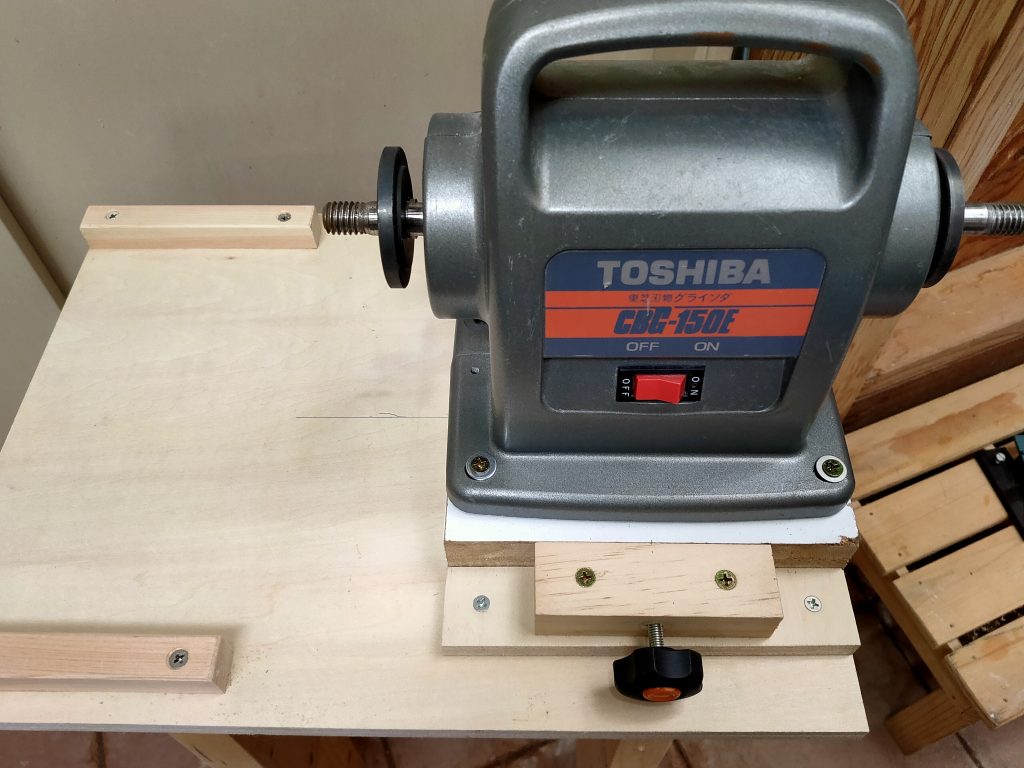
製作した土台にグラインダー本体を設置したところです。右下のボルトと鬼目ナットが合うように作りました。

ボルトで土台と本体を固定したところです。隙間なく固定できています。
ディスクサンダーを使用するときに土台をクランプで固定するために本体より大きく作っています。
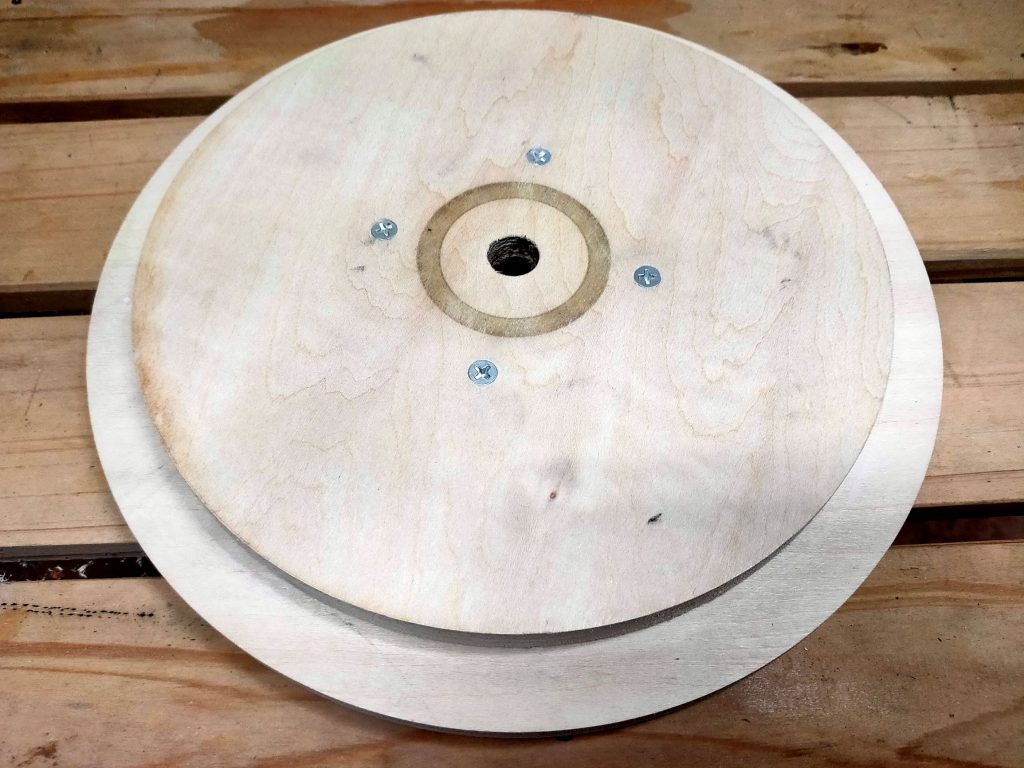
次は、ディスクサンダーのディスク部分を作成しました。ディスク部分は3層構造です。
1層目:ディスクと軸を固定するためのステー部
2層目:軸の固定ボルトを隠すためのスペーサ部
3層目:サンドペーパーを貼り付けるサーフェス部
写真は、上から1層目、2層目になります。
1層目の軸穴径は、本体の軸径とゼロクリアランスにして、回転時にガタつかないようにします。
2層目のサイズが、ディスクサンダーの研磨可能領域、必要なサンドペーパーのサイズ、本体の軸と土台までの寸法、そして土台の幅の寸法が決まる重要なパラメータです。かつ、ディスク部分の重量が装着されていた砥石重量を越えないようにします。正確には重量ではなくモーメントですが話を簡単にしています。最後にディスク部全体が3600rpmに耐えられる強度であることです。したがって、ディスクサンダーを設計する場合、最初に決める寸法になります。
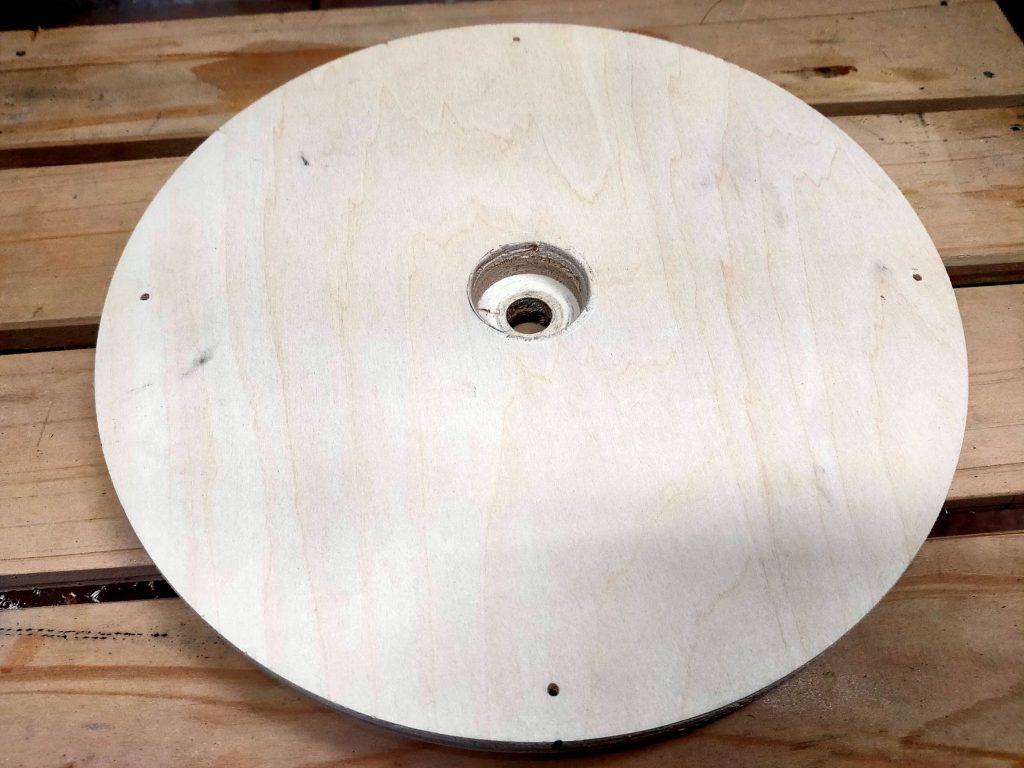
本設計では、どこでも入手可能で種類も豊富なサンドペーパーのサイズを元に決めました。
1層目:Φ 165㎜, t =12㎜
2層目:Φ 225㎜, t =12㎜
3層目:Φ 225㎜, t =4㎜
Φ:直径, t:厚さ
総重量:500g (< 砥石重量:715g)
材料:1,2層目:シナ合板,3層目:ラワン合板
合板は反りが出にくく、強度が高いので選択しました。
2層目は、ボルト部分のスペーサの役目なので、穴径は、ボルトをレンチで締められる径の寸法があればよいです。ただし、1層目と2層目の軸の中心は一致している必要がありますので、1層目と2層目の軸を合わせて木ネジで取り付けて置きます。木ネジでマークした上でそれぞれの穴を明けます。
この穴明けは、ディスクサンダーの動作時の安定性に大きく影響します。
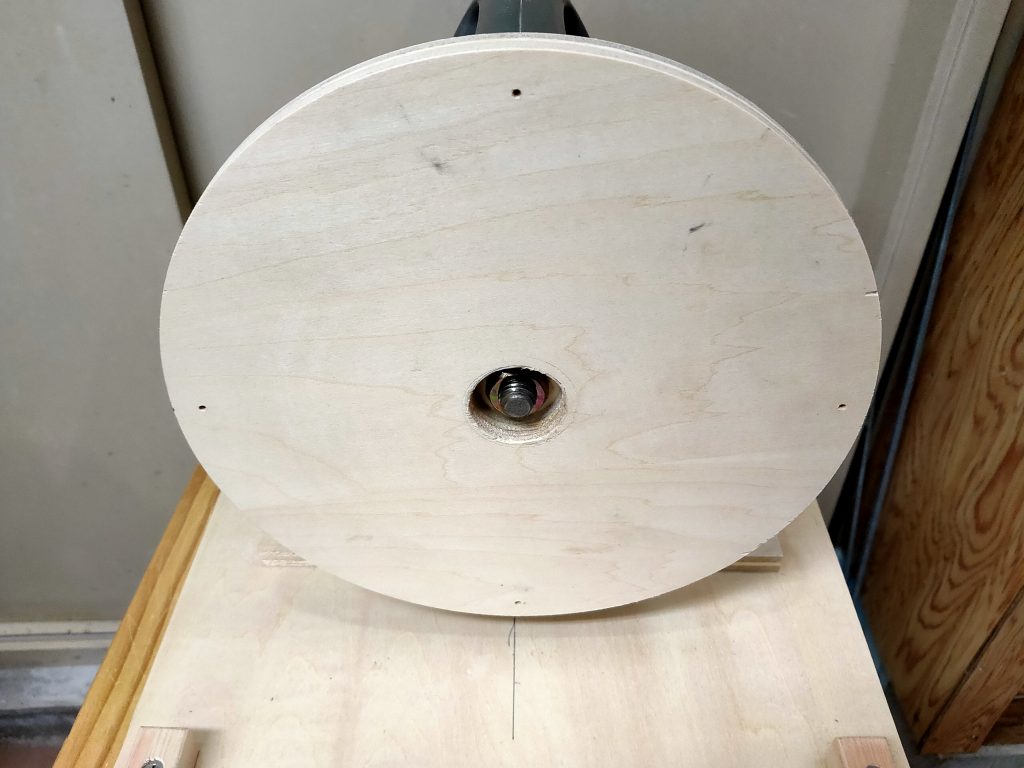
製作したディスク部を本体の軸に取り付けたところです。土台にも干渉していません。軸と土台までの寸法は、ディスク半径(112.5㎜)より大きくなるようにします。上述の通り、グラインダー本体下部に板を付けているのはそのためです。
また、写真ではわかりづらいですが、土台の幅は、ディスク部の直径より広くしています。
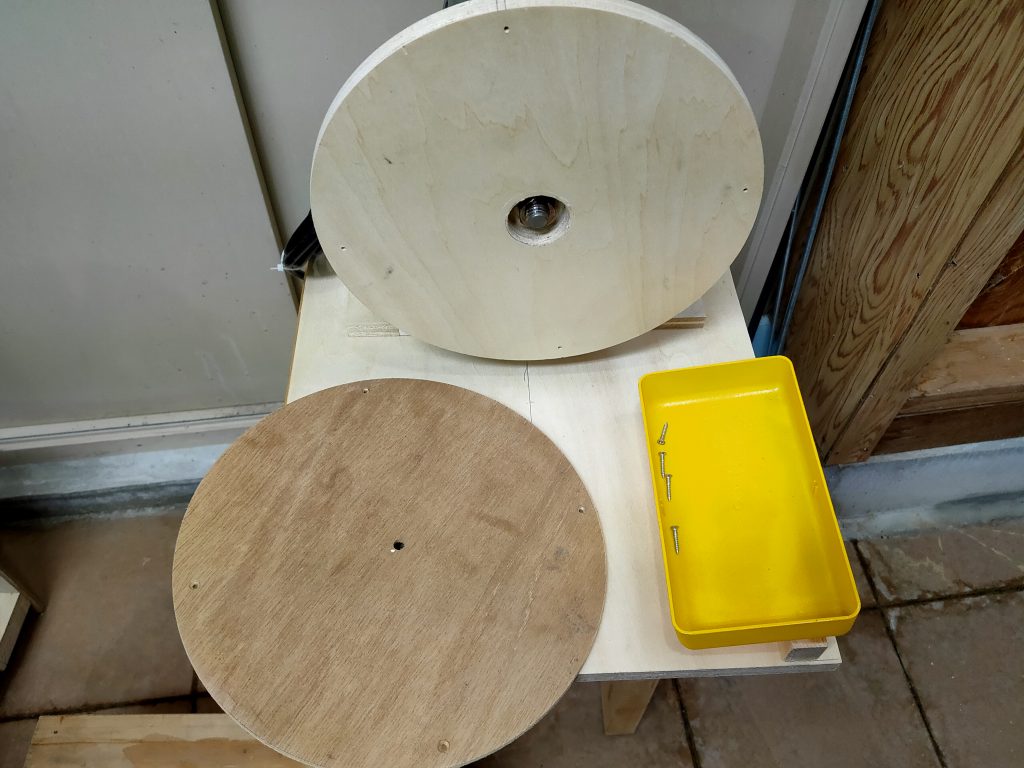
次は、3層目のサーフェス部の取り付けです。サーフェス部はサンドペーパーを貼り付ける部分になります。保守としてサンドペーパーの貼り換えが発生します。貼り換えでサーフェス部自体も表面が荒れてくるので交換できるように木ネジのみで留めておきます。
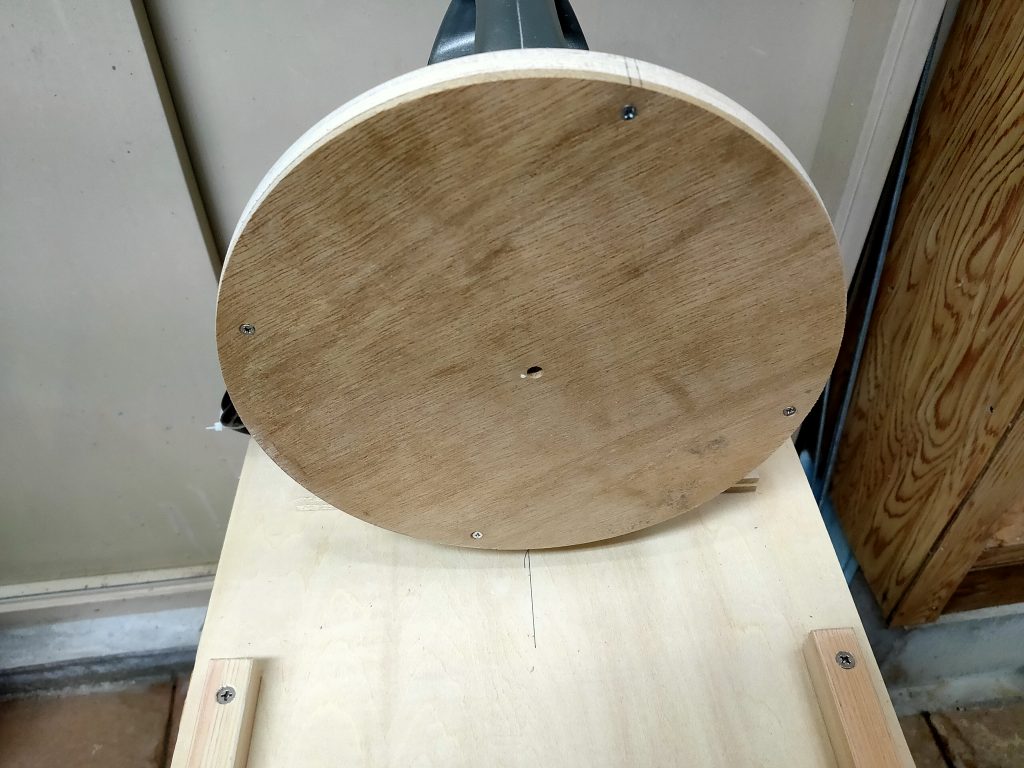
木ネジ、4点留めで取り付けたところです。
サーフェス部はラワン合板を使っています。これは表面がざらついており、サンドペーパーを接着しやすいように選びました。
サーフェス部に貼り付けるサンドペーパーは、写真の三共理化学製の「空研ぎヤスリ 10枚入」の♯240(240番)です。大きさは、230㎜×280㎜でディスクの225㎜に使えます。目の粗さは、「粗目」、「中目」、「細目」、「極細目」がありますが、♯240は、「中目」にあたります。木工などのニス塗り前の研磨にあたります。
「荒目」を使って、効率よく研磨することも選べますが、後で仕上げの研磨が必要になりますので、「中目」を選んでいます。
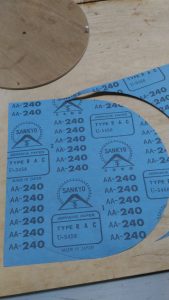
サーフェス部にサンドペーパーを貼り付けるので、サンドペーパーを円形にカットします。また、頻繁に取り換えるのは手間なので、紙ヤスリ(表面が茶色のヤスリ)ではなく、長持ちするものを選びました。
写真はサーフェス部を型紙代わりにして、サンドペーパーをカットしているところです。サーフェス部は予備を作っておくとよいです。
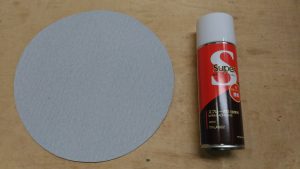
サンドペーパーは、スプレー糊で貼り付けます。糊をムラなく、程よい強度で貼り付けられるのでちょうどよいと思います。
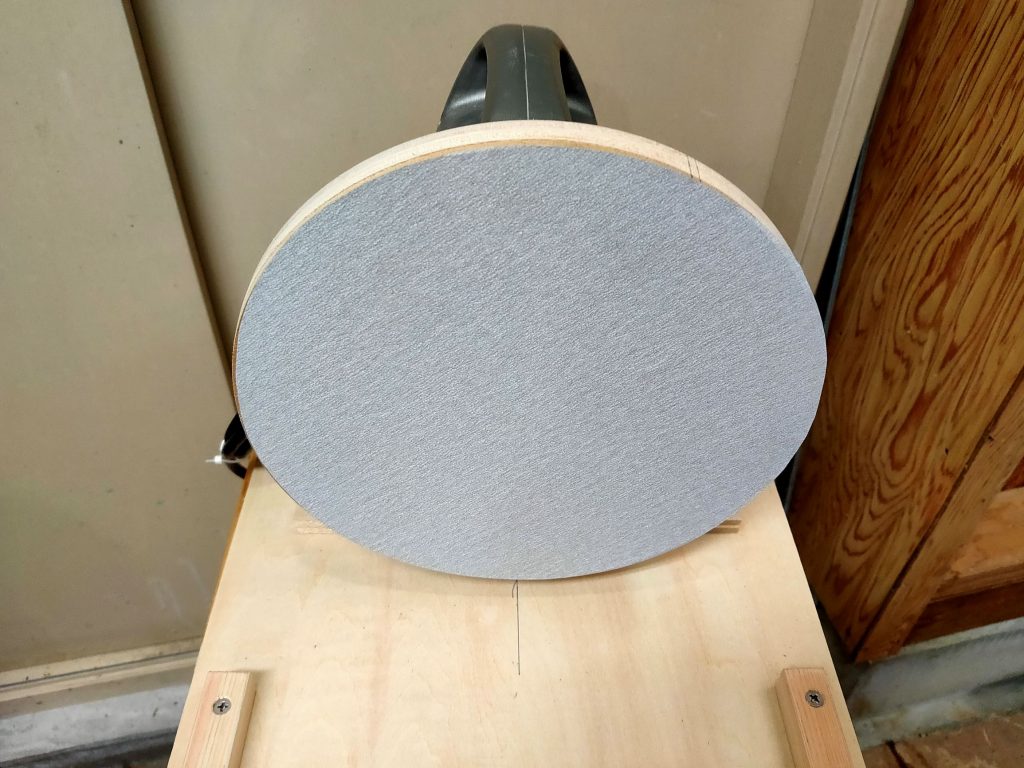
サンドペーパーをサーフェス部に貼り付けたところです。ディスクサンダーぽっくなってきました。
最後に大切なやることがあります。バランス調整です。身近なところでは、タイヤ交換したときにバランス調整してホイールの内側に重りが付いていると思います。それと同じことを、してやる必要があります。
ディスクの重量バランスに偏りがあると、高速で回転した場合、大きな振動になりグラインダーの軸が曲がったり、最悪の場合、グラインダー本体飛び跳ねたり、ディスクが破断して怪我の危険があります。
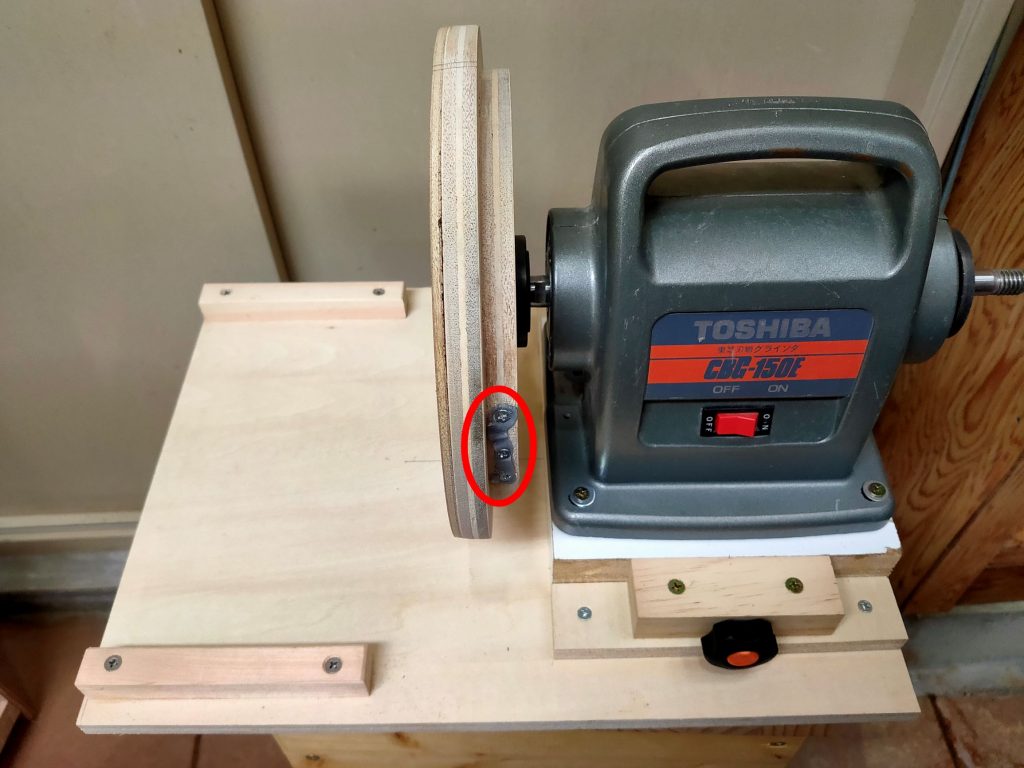
調整作業は簡単ですが根気よく丁寧にします。
バランスが取れているかは、ディスクを任意の位置に止めたとき、その位置にとどまっているか、動き出していつも同じ位置で止まるかを見ます。動いていつも同じ位置に止まる場合、止まったディスクの下側が重いということです。その場合、反対の上側が軽いので重り(バランサー)を付けてやればよいのです。どれぐらいの重りを付けるかは、上述の作業を繰り返えし、少しずつ重りを増減して調整します。ここでは鉛を重りとして調整しました。写真の赤丸で囲ったところにつけています。
重りをディスクの周囲(外側)につけているため重りをネジ留めしています。両面テープなどテープだけで留めるのは危険です。最初は良さそうに思いますが、遠心力で剥がれてきます。そして、最後には剥がれて鉛が弾丸のように飛んできます。自分もやらかして怖い目に遭いました。
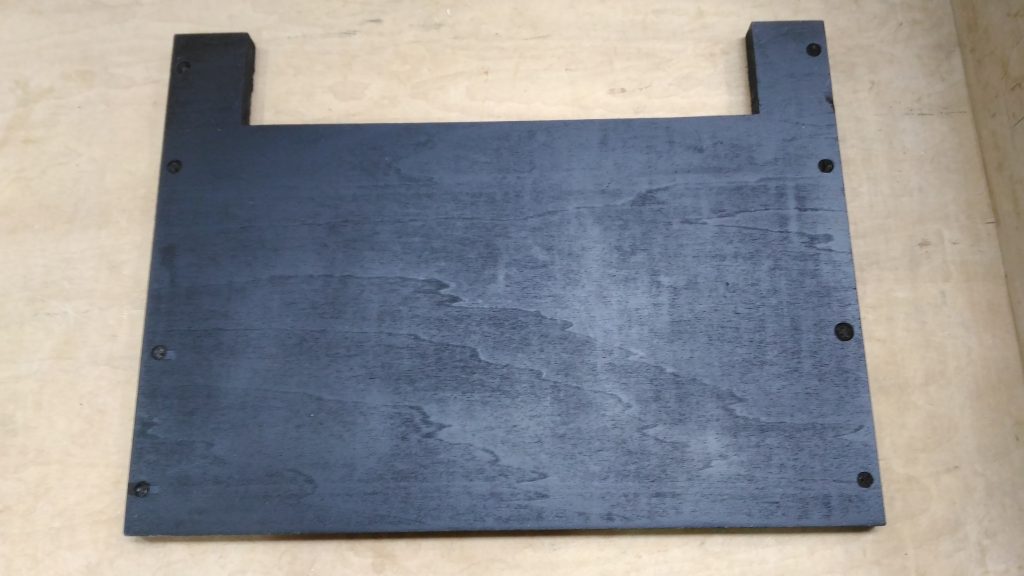
このままでは、作業がしづらいのでディスクの前に作業台を付けます。写真は加工した作業台です。写真上部の凹んでいるところにディスクが収まります。作業の視認性がよいように黒色で塗装しました。
土台製作時には、この作業台の大きさも考慮して土台寸法を決めています。
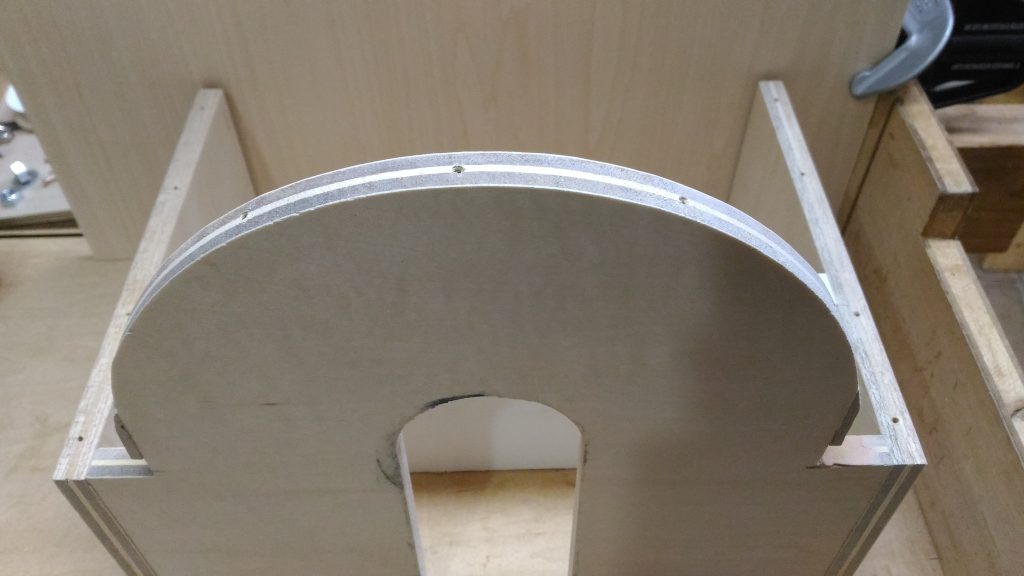
作業台のフレームを製作しました。フレームは回転するディスクが人に触れないように覆いになるように作成しました。写真前面に見える扇部分はグラインダー本体とディスクの間に入り、ディスク裏面が触れないように覆うようにしています。写真側面は、ディスクの下半分が触れないように覆うようにしています。フレームの上部はディスクがむき出しになっているので、ここにもカバーを付けます。
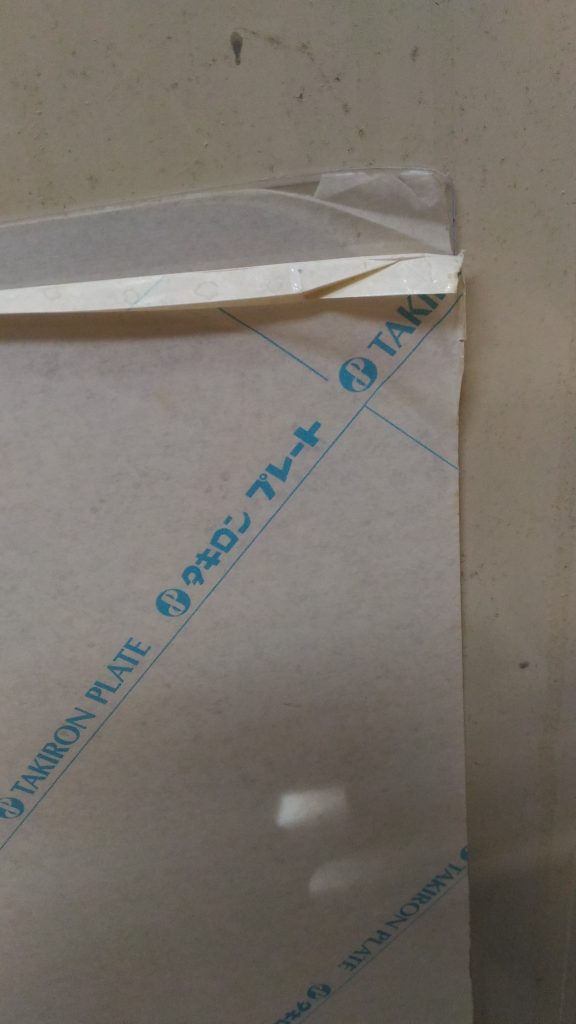
たまたま、工房にあったタキロンプレート(商品名)の硬質塩化ビニル樹脂板を使って、カバーを作成しました。元々は、カブト虫やクワガタ虫の大きな昆虫ケースを作るために購入したもので、その残りです。
名称通りで厚さ1㎜ですが、非常に硬くカッターではなかなか切ることができませんので、テーブルソーで切っちゃいました。テーブルソーで柔軟性のなる薄板を切るのは、巻き込みや割れなどの恐れもあるので板切れに両面テープで貼り付けて、板ごとカットしました。
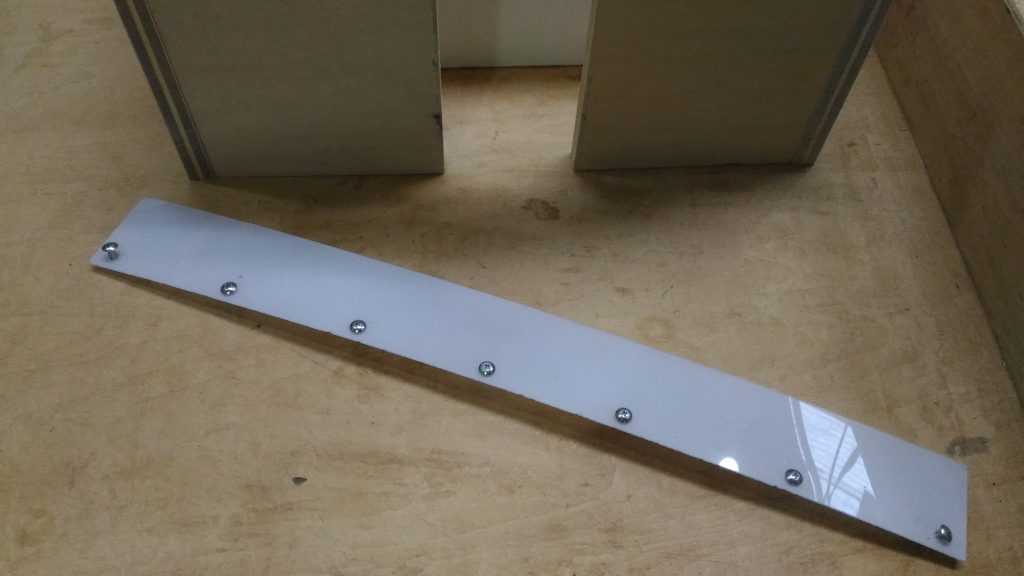
樹脂板をカットして、裏面を白色スプレーで塗装しました。また、扇型のフレームにフィットするように取り付けるため間隔を狭くしてネジを取り付けました。
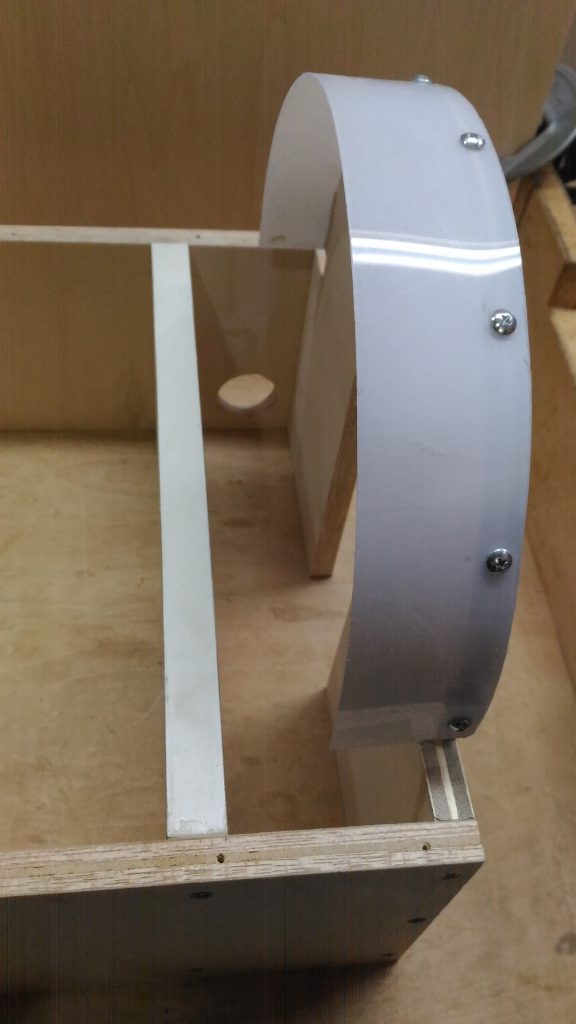
作成したカバーをフレームに取り付けたところです。硬質樹脂なので曲げたときに割れないか心配しましたが、杞憂に終わりました。作業台の黒とカバーの白でコントラストがよく、映えると思います。
フレームの中に仕切りを入れています。これは、研磨くずが仕切りの中に納まり、奥につけた穴に集塵機のホースを付けて、研磨くずを吸い出そうと考えたからです。
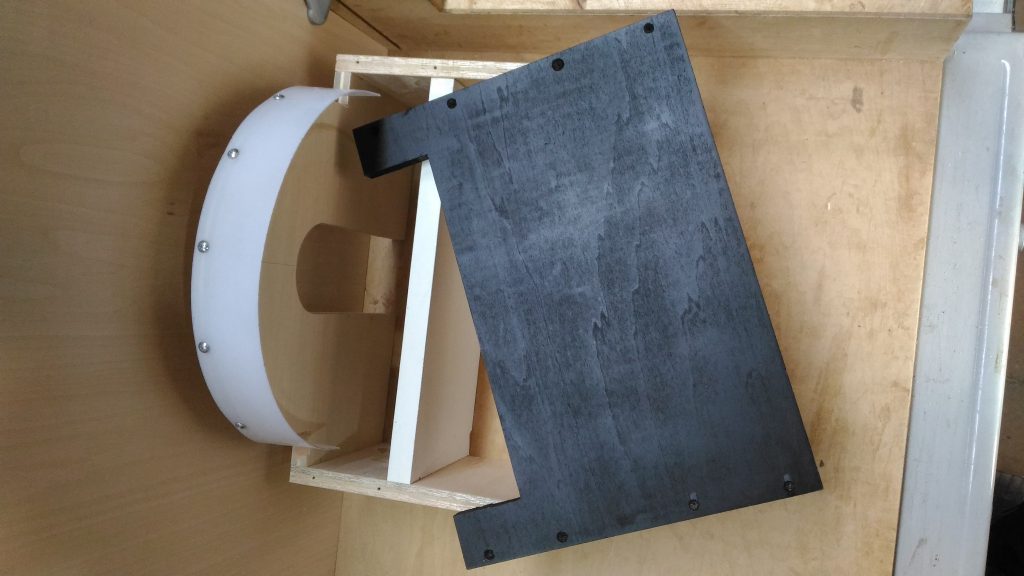
フレームに作業台を取り付けます。
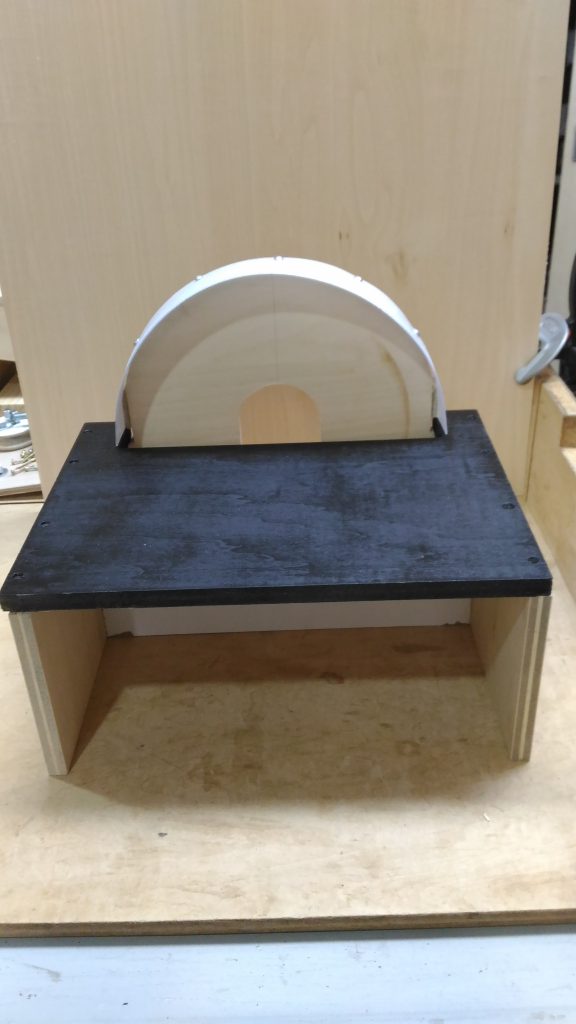
作業台をフレームにネジ止めして完了です。
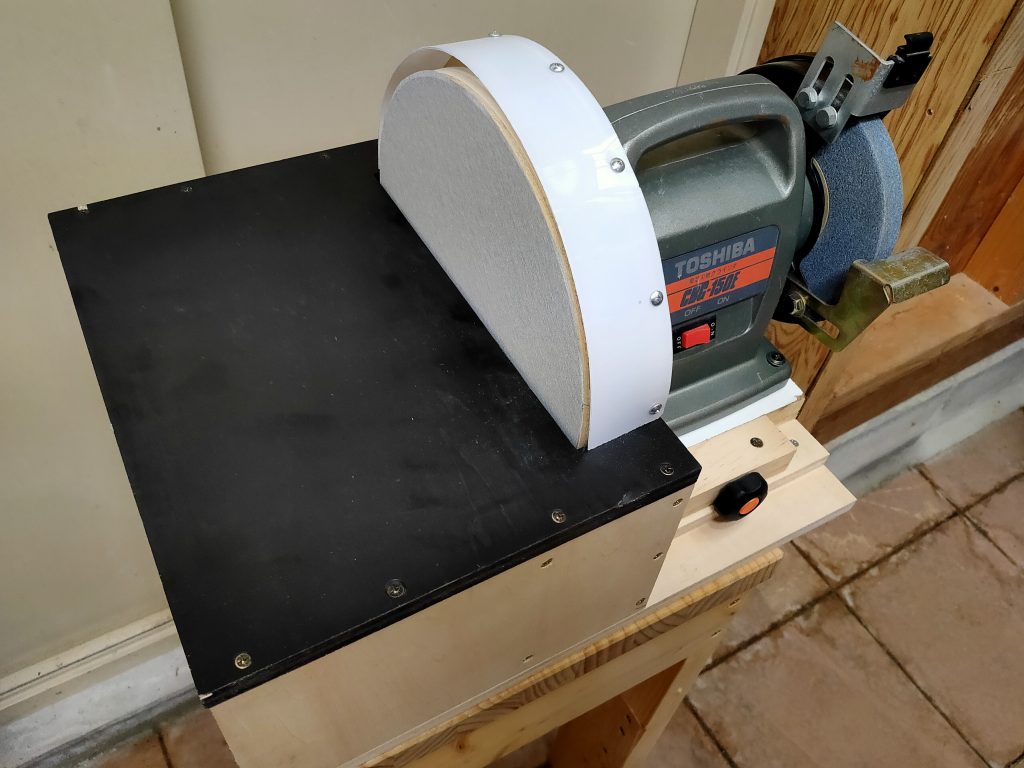
グラインダー本体に上から被せたところです。作業台フレームは本体に被せているだけで、特にネジ留めなどはしていませんが、ずれたりせずぴったり収まっています。上述の土台の写真を見ていただくをわかりますが、木片のフランジを付けており、このフランジと作業台フレームの内側がぴったりはまるようになっています。
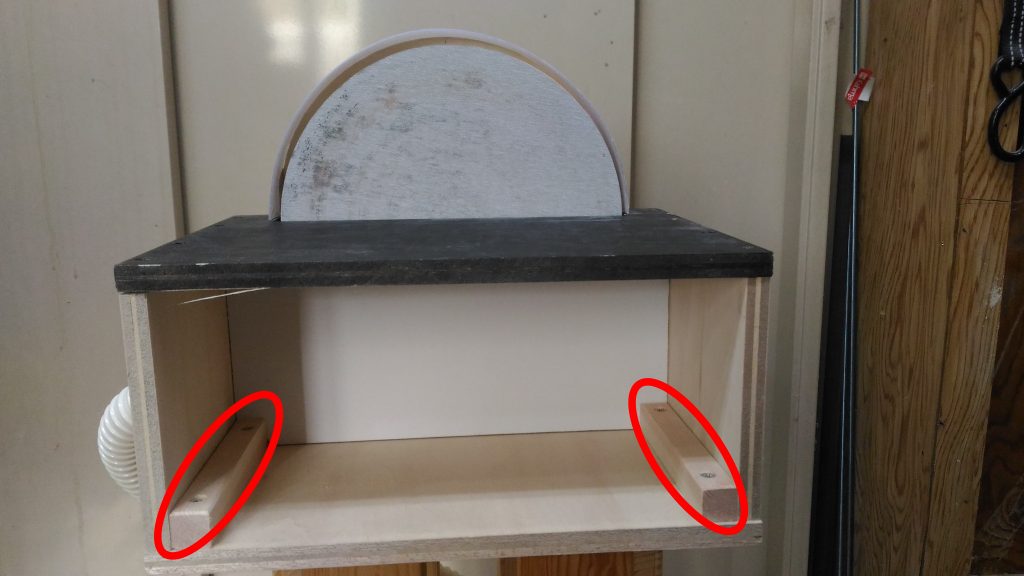
写真赤丸の土台のフランジが作業台フレームの内側にぴったりはまっているのがわかると思います。作業台フレームの裏面は、グラインダー本体下部の板面にちょうど当たるようになっているので、上方向以外は固定されるようになります。
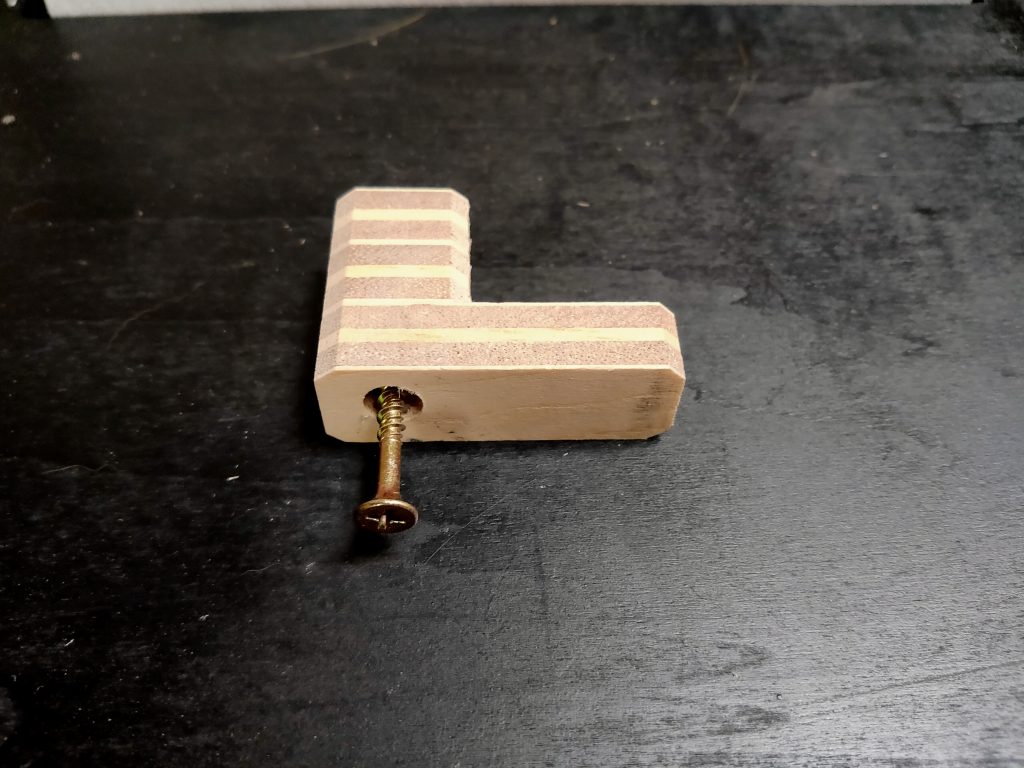
電源ケーブルは長いので、使わないときは巻き取っておけるようにケーブル固定サドルなるものを自作しています。合板の切れ端を使って3つのピースで作っています。長めのピースと短めの2つのピースを木工ボンドで接着しています。
作るときには、何個か作ってまとめ置きしておきます。ケーブルを巻き取るため2つでひと組です。
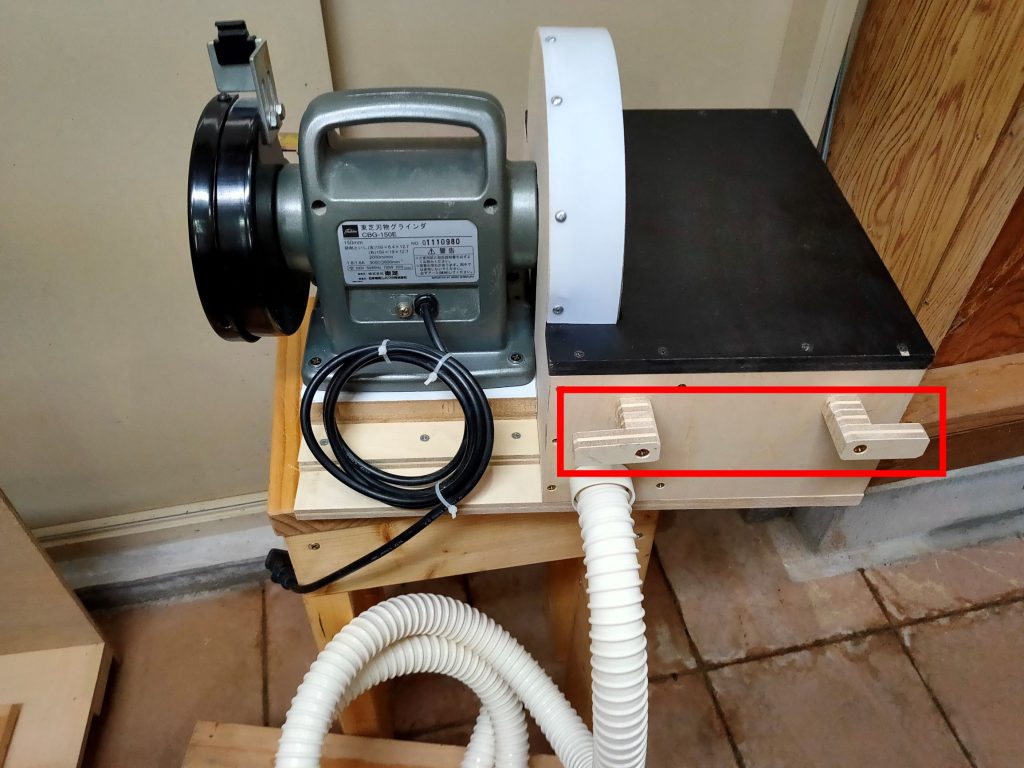
写真赤枠の部分に電源ケーブル固定サドルを2つ付けました。付けるときは木工ボンドとネジで固定します。ネジだけだと、サドルが緩んでしまいます。
左側サドルの下に、ホースを取り付けています。作業台フレームに集塵ホース用の穴を明けていましたが、そこに集塵用のホースをはめ込んだ状態です。集塵用ホースといってもホームセンターで洗濯機の延長ホースとして売っているものです。
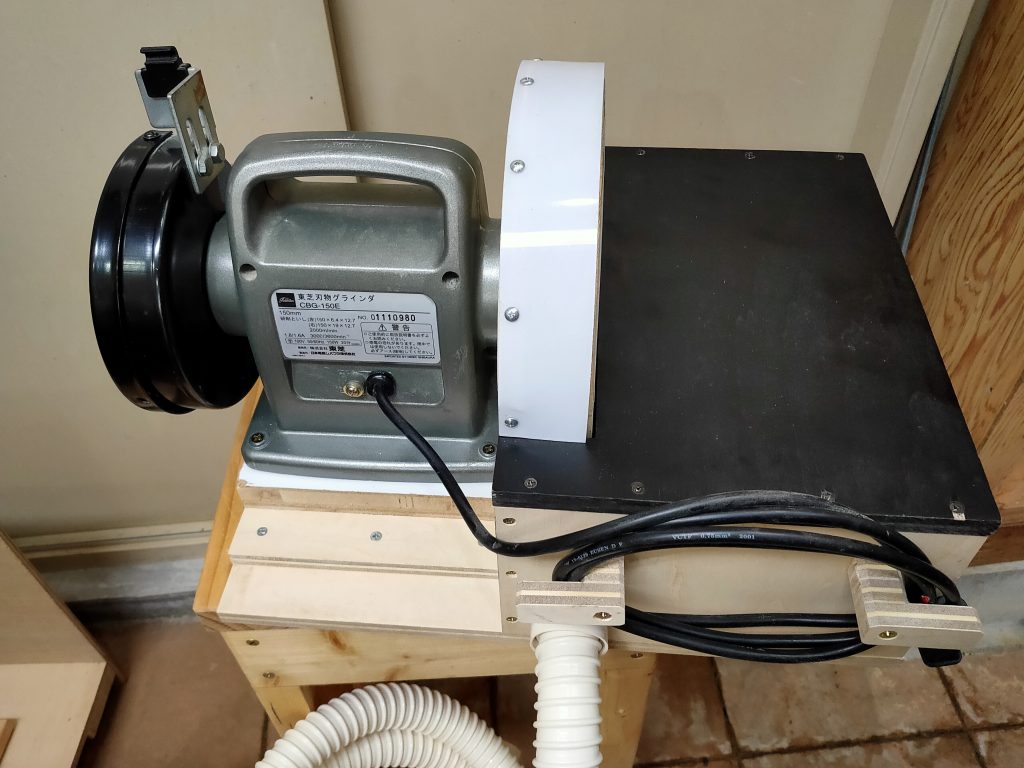
サドルに電源ケーブルを巻き付けたところです。ちょうどケーブルのプラグがサドルのところにひっかり収まりがよいです。
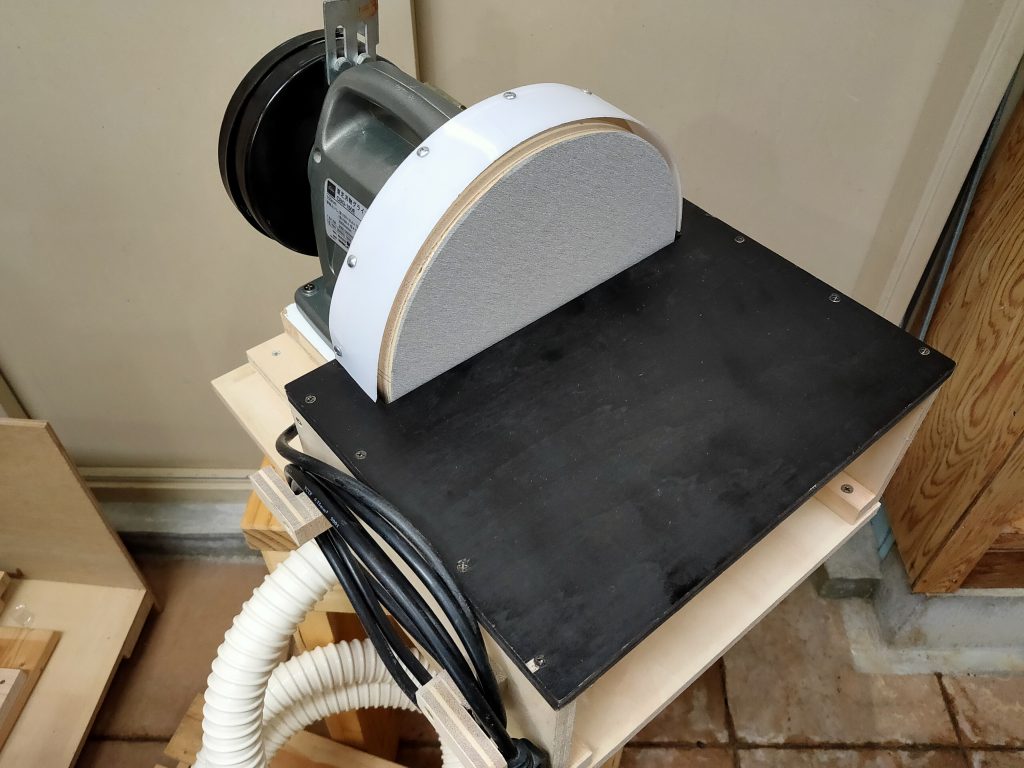
ディスクサンダーの自作の完成です。
実は、ディスクサンダーを製作途中でも、ディスクサンダーを使っていました。上述の電源ケーブル固定サドルの面取りは、このディスクサンダーで研磨しています。
研磨作業の時にディスクの外側を使いすぎると、負荷が大きくなり回転速度が落ちるので、落ちてきたら被研磨部材を離して負荷を下げてあげる必要があります。これはグラインダーとして使用しているときも同じです。
最後に言うまでもありませんが、グラインダー以外の使い方なので、自作は自己責任ということです。